Data Driven Fretwork
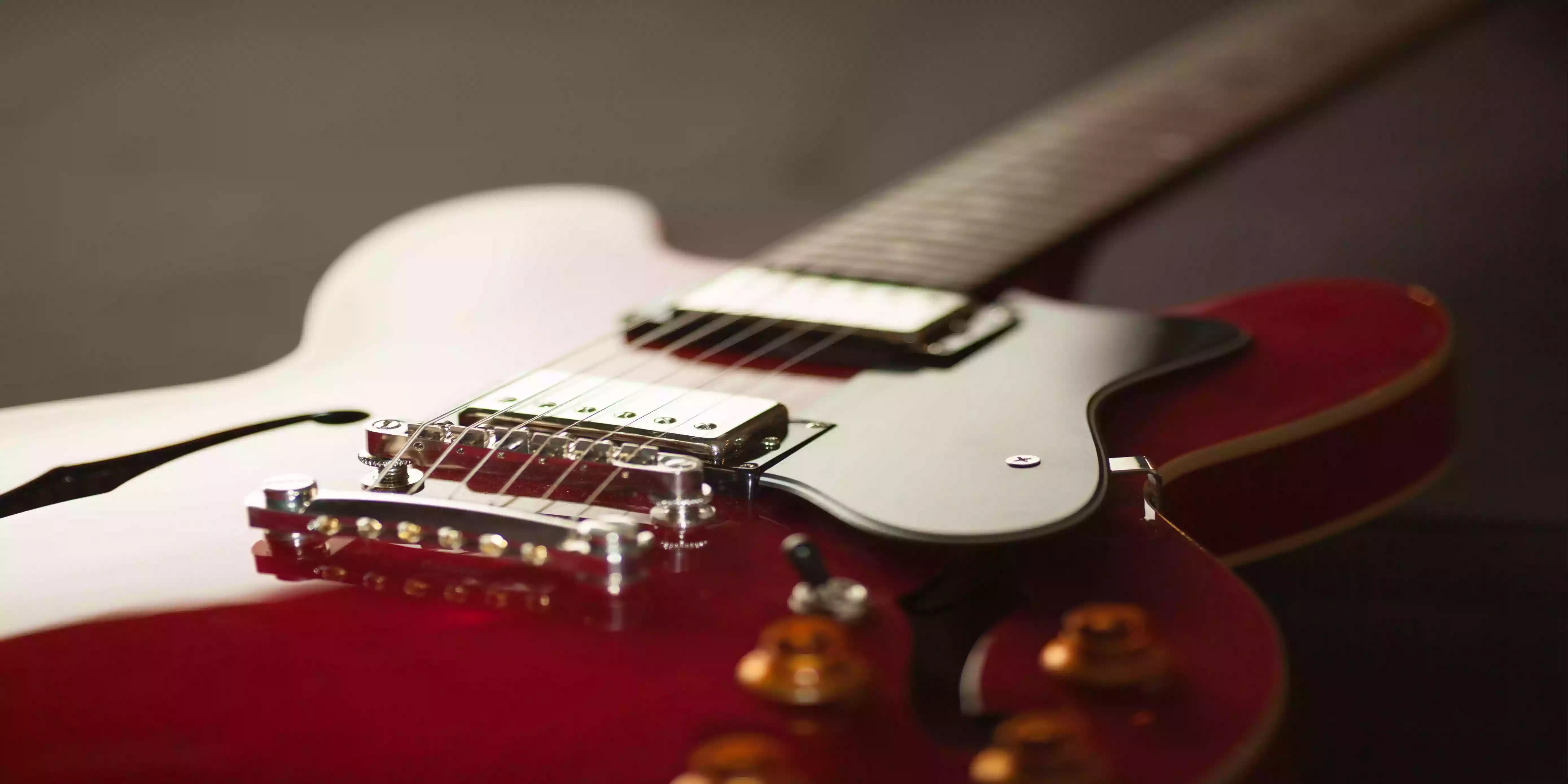
A guitar tech’s take on PLEK
The PLEK Station is a specialized robot that creates a high-resolution digital scan of a guitar’s fingerboard and performs fully automated fretwork. The machine collects data about the playing surface, recommends fret adjustments for optimal performance, then cuts the frets with perfect precision.
The robots are coming!
In 2017, Yorkville Sound purchased a PLEK Station fret leveling machine to perform quality control on the guitars they distribute. Yorkville began offering PLEK services to Long & McQuade customers as well, providing our guitar techs access to the most advanced technology in our industry. Reactions were a mix of skepticism and excitement… and a remote fear of a super-intelligent A.I. destroying humanity for not humidifying their acoustic guitars in the winter!
After two years, I wanted to share my thoughts on the whole journey.
Old craft, high tech
Like many on the guitar repair team, I had mixed feelings at first. On the one hand, I felt strongly that traditional methods done properly could be as accurate as the PLEK process. However, fretwork requires meticulous consistency and has little room for error. When something requires “machine precision,” robots obviously offer a potential advantage.
There’s also an added health and safety advantage. For years, I’ve watched guitar-techs labour through the repetitive motions of traditional fretwork, filing, sanding and polishing by hand, often for hours in a single day. This can cause repetitive stress injuries, and the long-term health benefits of removing that physical stress are potentially life changing.
Fears of a robot apocalypse may have been overstated
This robot is not actually taking anyone’s job. Like any tool, it allows you to do a job more easily and effectively, but it doesn’t do all of the work for you.
The software makes suggestions, but the result will only be as good as the person operating the machine. The technician must have the fundamental knowledge of how fretboards work and how vibrating strings behave in order to make the right decisions.
Rather than replacing human capital, PLEK Station has magnified the value of that fundamental knowledge. We chose to have our machine operated by our most experienced fretwork technicians, and their knowledge and experience of traditional fretwork is employed on every guitar.
As for the actual quality of the result, my original assessment of the technology proved to be basically correct. PLEK is no more precise than traditional methods performed by a skilled expert. Both approaches can result in a fretting plane that is accurate to within .025mm, and traditional finishing touches like hand polishing are still needed after the PLEK has done its job. A redeeming fact for the traditionalists: it turns out we’ve been able to get things “good enough for rock and roll” since before rock and roll!
It’s all about data
As with many things these days, data is of extreme value and this is where the PLEK Station presents its greatest advantage.
The PLEK records more information in its initial scan than a luthier could in an afternoon of taking measurements. The height and spacing of every fret are measured beneath every string path: right there you have 252 individual measurements. It measures the fingerboard radius at every fret for another 21 measurements. It also measures string spacing at the nut slots and the bridge, the relief of the fingerboard and even the flexibility of the neck. All of this data is compiled into a high-resolution 3D model of the fingerboard in a few minutes.
Before scan After scan
There isn’t a guitar technician on earth that would do this kind of analysis by hand, and having this additional data will allow us to make better decisions for your guitar.
What it means for technicians and players
The advantages of the PLEK Station for technicians are huge: We can get a result that is as good as ever, with less physical pain and more certainty in the result. What’s not to love?
But what about the value for players?
For 99% of players, fretwork needs to happen from time to time. If the natural aging of wood doesn’t cause your neck to drift out of alignment over time, the slow wearing away of your frets will eventually require correcting. When deciding between PLEK and traditional methods, there are a few aspects for the player to consider:
Nothing is Lost: At Yorkville, the PLEK process is performed by a skilled technician with a strong background in traditional fretwork. All of the knowledge and care of the traditional service remains and is simply enhanced by this new technology, so nothing is lost by choosing the PLEK service over a traditional approach.
Clarity: Traditionally, a neck is first assessed by sighting (looking down the neck with a well-trained eye), and precision measurements may also be taken using machinists’ measuring tools like straightedges and feeler gauges. For the player, neither method is easy to understand, and professional techs sometimes disagree with what they see when sighting a neck. Optical illusions can sometimes make a twisted neck look straight or vice-versa.
The PLEK makes this process both objective and accessible. The scan produces visuals that can be easily understood by anyone. Little to no explanation is required to see if a fingerboard is warped or twisted, and the player can even see the before and after scans to see what was changed.
No special voodoo is required to understand what’s going on with your guitar... I wish my mechanic had this!
Repeatability: PLEK saves every scan it creates for later recall on any machine, anywhere in the world. This means that if you have your guitar PLEK’d, and a few years later it’s time for more fretwork, we can make exactly the same adjustments as last time. If you have two similar guitars for which you want to have identical fretboards, that can easily be done.
Mental Ease: No guitarist wants to wonder if their gear is holding them back.
When you get a bit of string buzz you want to know, “Was that me or was that the guitar?” Putting your guitar in the hands of a competent and experienced guitar tech should alleviate this worry no matter what methodology they are using. That said, when I can see and understand the state of my fingerboard with total clarity, measured by an objective machine, it sure takes a load off my mind.
Knowing that things are working as intended makes you a better musician because you can stop thinking about your gear and focus on the music.
Stronger together
In the end, the T-1000 of guitar repairs is not coming for my job any time soon. Without the operator’s deep understanding of fretwork theory and practice, this machine offers very little value. But combine this technology with an experienced tech and you have an unbeatable combination.
I think it will be a long time before robots are doing all our guitar tech work, but the day is upon us where robots are being used to enhance the abilities of humans, even in this obscure little corner of the music world. I don’t see a future where we could ever go back.
In closing, I see this being somewhat analogous to digital tuners:
Do you absolutely need it to get the desired result? No.
Is it going to get flawless results if you have no idea how to do it the old fashioned way? Likely not.
Does it enhance the user’s current abilities, making the task easier and more consistent? Definitely.
Are guitar players around the world getting better results by combining new technology with traditional skills? Undeniably.
If you would like more info on the PLEK service, I encourage you to visit the Long & McQuade Musical Instruments YouTube channel where we feature an in-depth video of the entire process.
www.youtube.com/longmcquade
Check out our first article on PLEK - PLEK: The Best Your Guitar Can Be
***
Mike Robicheau is a lifelong musician and has been building and repairing all types of fretted string instruments for 12 years. Following a career performing and teaching guitar in Nova Scotia and BC, he moved to Toronto in 2009 where he now manages Long & McQuade’s nation-wide team of guitar technicians. He can often be found at the Bloor street location helping diagnose tricky repairs and delivering long-winded monologues on various aspects of guitar design and construction.