The Right Cymbal For You
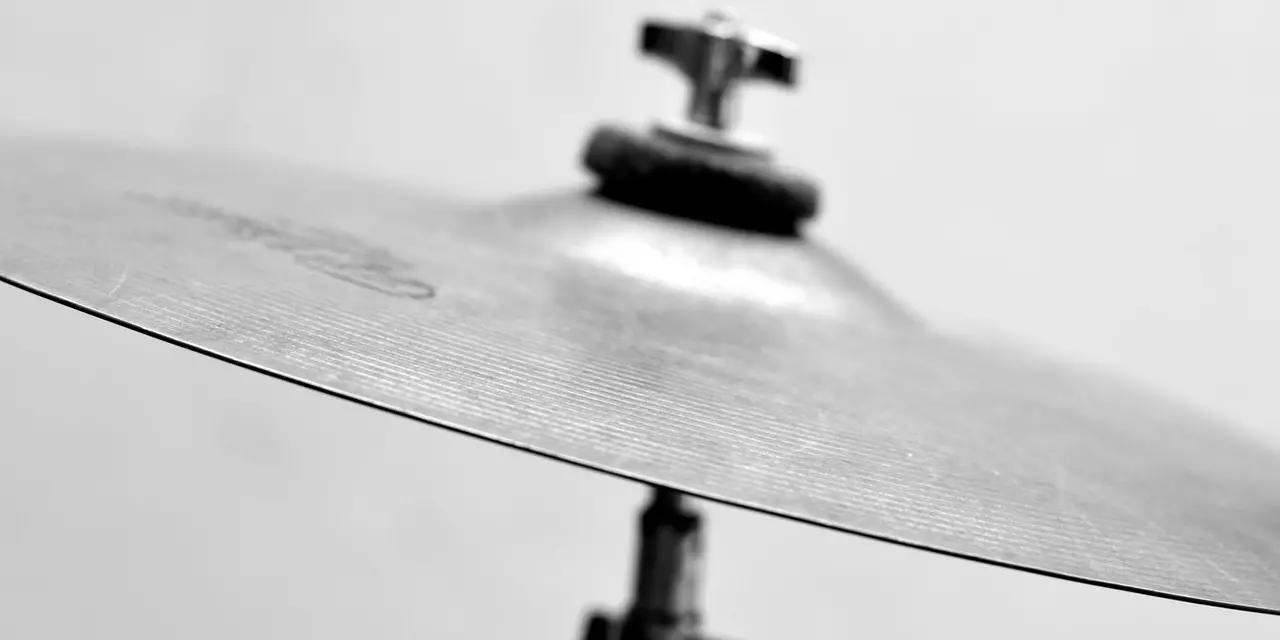
It can be quite intimidating to walk into a music store and see rows upon rows of different cymbals hanging on the walls. You may ask yourself, “How do I know what I am looking for?” There is a lot that goes into the art of cymbal creation: different metal working techniques, different finishes, and even different alloys. Different applications, such as live or in studio, also affect the different types of cymbals one should use. It is very important for you as a drummer to know what you need before you pick out your first cymbal set.
Different Alloys
Brass cymbals often have a yellow tint, and produce a sound that could be described as warm, and slightly dull in nature. These cymbals are made from sheet metal, and are often included in beginner drum kits, or individually as inexpensive cymbals. For a beginner drummer they are ideal.
B8 bronze is created with 8% tin and 92% copper, a composition commonly used in bronze cymbals such as Sabian's B8 line and Zildjian's ZBT line, which are more affordable to the average buyer.
Some other cymbal companies have used this alloy to create higher-end lines, such as Paiste's 2002 and Giant Beat lines, which are both made from B8 bronze, and are amongst their more popular professional lines.
B8 bronze is a very strong alloy, which allows it to be stamped and formed from sheet metal. This produces a cymbal with a very distinct tone to it, which is preferable for louder genres, such as rock and metal, as it blends better with the multitude of frequencies being produced.
B20 bronze is the other common alloy, created with 20% tin and 80% copper, and sometimes traces of silver. The more tin involved, the more malleable the cymbal becomes. This is not a negative quality, however, as it provides the cymbal with more overtones which can be more musical in settings that require more technical playing. Even in more basic musical settings, these cymbals can still be appreciated. One might be worried about the higher tin content making the cymbal more susceptible to breakage due to the increased malleability, but when struck with a drumstick, these cymbals absorb the impact better which can help extend the life of a cymbal. Rather than being stamped, these cymbals are cast, as the alloy is more fragile and cannot be formed as easily into sheet metal.
Check out this brass cymbal, the Sabian SBr 16 Inch Crash, this B8 bronze cymbal, the Paiste 2002 18 inch Crash and this B20 bronze cymbal, the Meinl Byzance Dark Crash 18 inch.
Manufacturing Techniques
Sheet cymbals are cut from large sheets of metal. Most commonly, these types of cymbals are made from inexpensive alloys as they require a stronger metal to form sheets, and as mentioned before, less expensive alloys produce stronger metals. Cymbals manufactured using this process require less time and less labour, and are commonly thought to be cymbals of less quality. However, some cymbal companies, such as Paiste for example, use this manufacturing process with all of their cymbal lines and manage to produce some of the most professional cymbals on the market.
Cast cymbals are created by pouring molten metal on a slab and rolling it to flatten it. It is shaped, the bell stamped in, and the centre hole cut. The cymbal then goes through a hand hammering process. These cymbals are considered professional grade, as they require a lot of labour intensive work, and much care is put into the processing of these cymbals. All high-end cymbals are made using this process, with few exceptions.
Hand hammering is the process that cast cymbals go through after they are cast into shape. Manufacturers do one of two things to complete this process; they either use a machine to evenly hammer the cymbal throughout so that the weight of the cymbal is balanced all the way through, or they hammer it by hand with random distribution. When a cymbal is hand hammered by a machine, the even distribution of weight allows sound waves to vibrate faster when the cymbal is struck as there is less impedance, which lets the cymbal pen up faster and makes the pitch brighter. Uneven hand hammering inhibits and slows down the vibration of the sound waves due to the fact that the cymbal is more difficult to travel through, making the sound of the cymbal much darker and lower pitched. Lathing, or turning, is another common post-shaping technique where tiny ruts are cut into the cymbal, spiralling down its length. This takes weight off the cymbal and raises the pitch and brightness of the sound. Some cymbals are partially lathed, and some are left unlathed. Leaving parts, or all, of the cymbal unlathed can either keep the cymbal dark, or create additional undertones that are darker.
Here's a cast cymbal, the Zildjian A Custom 16 Inch Crash and here's a machine hammered cymbal, the Sabian HH 18 Inch Vanguard Crash.
On the Stage and In the Studio
It is important to know where and when to use different types of cymbals, and to make sure that your cymbal set matches your most common use.
Brass cymbals are usually too tinny and low-volume to take to a gig or to a studio, and generally bronze cymbals are preferred for both of these settings. This is not to discredit the use of brass cymbals, as they are wonderful to use for practice as they are a less expensive alternative to bronze!
When playing live, it is often better to play with cymbals that are brighter in nature. Cymbals that are thinner, made of B8 bronze, crafted from sheet manufacturing, lathed, or hand hammered by machine produce brighter tones and higher pitches. These can be ideal when playing for a crowd, as darker cymbals may get lost in the mix and sound murky. On the other hand, in the studio, darker cymbals may be more preferable. This includes cymbals that are cast, left unlathed, hand hammered by the manufacturer, or just thicker in nature. Under a microphone, these cymbals have less harsh high-end to them, and sound warmer and bigger.
In Conclusion
To a drummer, cymbals are a very personal piece of their drum set. It is their voice that they speak through, and it is crucial to be able to pick out cymbals that suit your wants and needs. It is a very big world, but hopefully this will give you insight into the unique nature of cymbals and their different sounds. For some, their taste lies with the more simple nature of a B8, machine pressed cymbal, and others prefer the deeply complex nature of a cast, hand hammered, B20 cymbal.
Simple, complex, bright, dark, sustain, decay: it's all your choice at the end of the day if you know what to look for!
Make sure to check out our other blog post, Choosing Cymbals: A Guide for the Beginner!
* * *
Michael Schroth has been working for Long & McQuade Waterloo as a Lesson Centre Coordinator since 2016 and has been an active musician for many years. In his personal time, he works on his own musical projects as a multi-instrument musician playing keys, guitar, and mainly drums as a Mapex-endorsed artist.